Rent or buy now!
A new benchmark in open maintenance access systems.
Our highly flexible maintenance system basic 1.1 enables fast and safe access for maintenance of rotor blades. Functions such as the ability to swivel the maintenance platform or move it sideways create real added value that is reflected in the quality of the rotor blade repairs, cost efficiency and accessibility for a wide range of different wind turbines.
By bringing together expertise gained with the maintenance system terra 1.1 and countless new technological innovations, the maintenance system basic 1.1 sets new standards for open maintenance access systems.
- Optimum access to the rotor blade is provided thanks to sliding floor panels and the ability to move the platform body sideways
- The flexible suspension system adapts automatically to the distance between the attachment points to ensure stable access
- Increased gangway width compared to conventional maintenance access systems
- Full rotor blade access all the way up to the root of the blade
- Transport in an ISO container (20 ft)
Sideways movement, sliding floor panels and swivelling of the maintenance access system.
In order to optimise working conditions even on open maintenance access systems, ergonomic considerations were placed at the heart of the development and fully implemented. When working at a great height, engineers must cope with a working situation that is highly complex and demands a great deal of attention at all times. The System basic 1.1 is designed so that the access system itself is incredibly simple to use, in turn making it as easy as possible for the repair engineer to safely carry out repairs to rotor blades.
- With the ability to swivel and move the working area sideways (with electric, stepless adjustment), the blade tip is always easy to reach (see graphic below)
- Spacious working conditions with a wide gangway and overhead attachment of PSE to a lifeline
- Inside railings are lower than the outside railings – for a more spacious working area inside and better protection on the outside
- 360° access to the rotor blade is possible
- Sliding floor panels for access at the rear edge
- Minimised set-up time
- Lighting kit for working at dusk or in poor visibility conditions (floor/stand-mounted lighting)
Swivelling out to capture the rotor blade tip
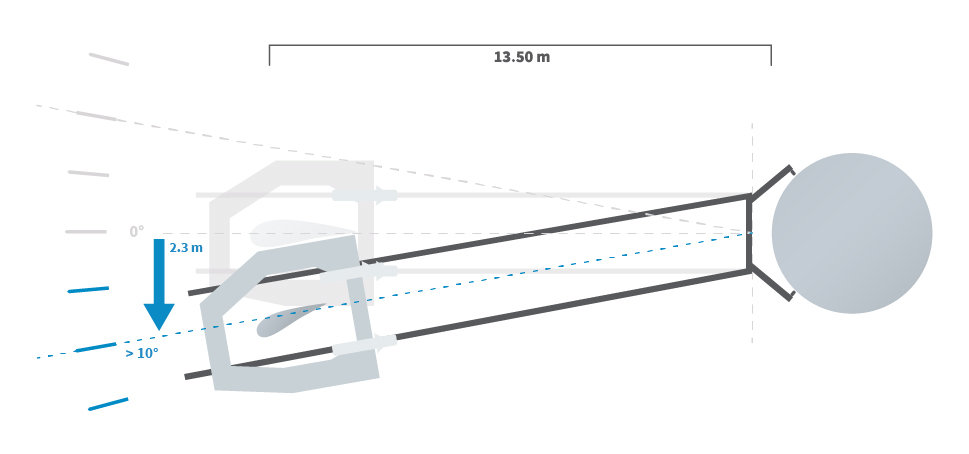
Stepless electric adjustment for sideways movement of the platform
With the aid of the horizontal adjustment options for the working area, which permit a maximum movement range of 1 m, the system enables incredibly flexible working on the rotor blade.
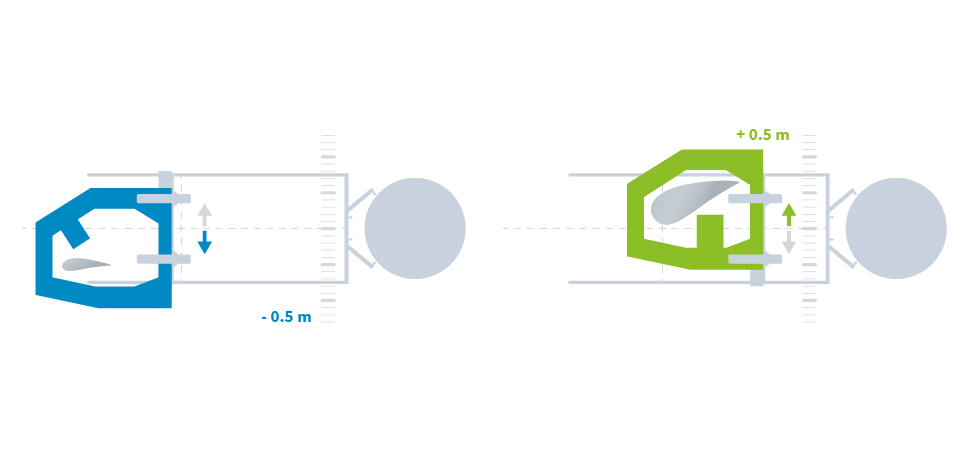
Monitoring with sensors, tilt adjustment and the self-adjusting suspension system.
With a large number of safety features, this maintenance access system also sets new standards in terms of occupational health and safety. The sensor systems installed monitor the load distribution depending on the positioning of the support frame and the suspension system and check important parameters such as the horizontal forces due to the stay cables and the wind loads.
- Self-adjusting suspension system (lateral direction – passive); possible width between suspension points ranging from 1,7 m to 4,0 m
- Tilt adjustment (active) in longitudinal direction
- Monitoring of the cab payload (additional function for limiting the lifting force of the winches)
- Automatic monitoring of the horizontal forces due to the stay cables (to avoid excessive load off the pushing frame)
- Automatic tilt adjustment for safe working on the open maintenance system basic 1.1
- Thanks to electric adjustment of the suspension point, the user can adjust the required tilt of the maintenance access system
Self-adjusting suspension system
This innovative system offers great flexibility for attaching and securing the open maintenance access system basic 1.1
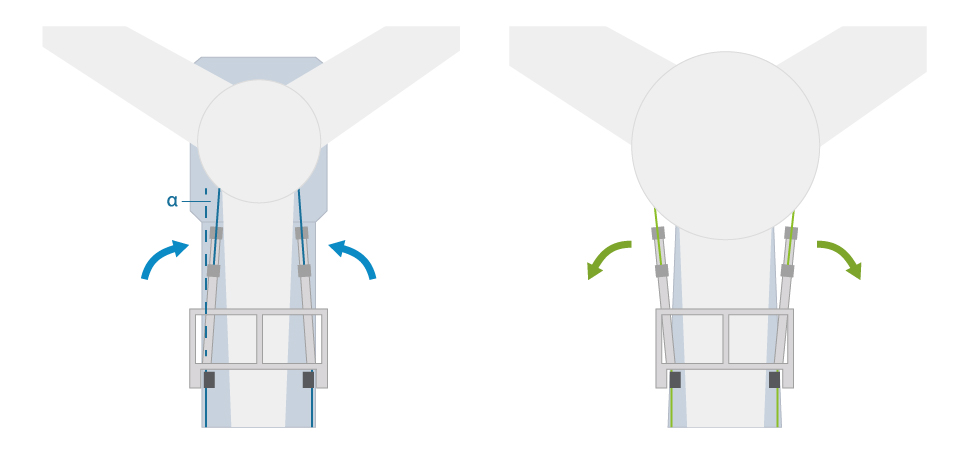
Manual tilt adjustment
The manual tilt adjustment ensures safe working on the open maintenance system basic
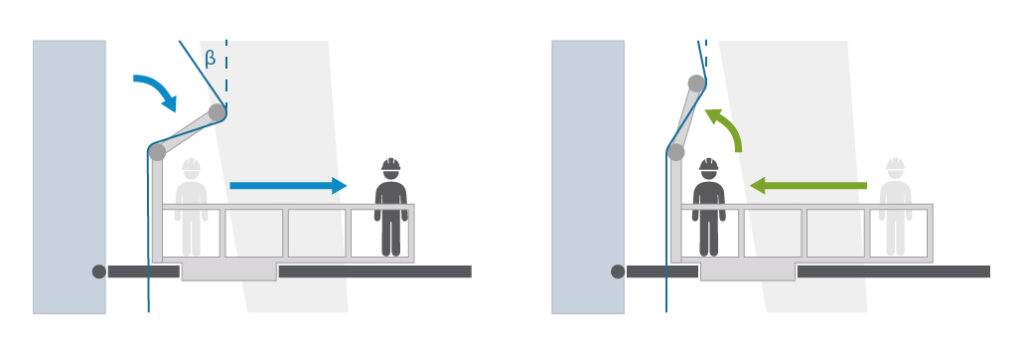
All functions and messages from the system at a glance
System errors are signalled to the operating staff with the aid of audible signals and flashing codes on the LED display. Together with the intelligent remote control system, this provides users with a comprehensive control system.
- PLC-based safety system – state of the art controls with robust sensor systems
- Control via remote control (wireless optional)
- Faults are displayed via LED flashing code
Ready to use. Simple to transport.
The design of the maintenance cab in the System basic 1.1 enables efficient set-up/tear-down with a simple locking mechanism on the specially developed 3.5 t trailer. Stowage options for all mounted parts and a generator (available on request) are integral parts of the trailer.
- Simple, efficient assembly and disassembly
- Optional accessories such as an infrared heating unit, lighting kit, shelving system, temperature-controlled chemicals box and a hand winch round off a product where all your needs are covered
- Almost all the accessory parts are transported on the trailer, so no additional loads are placed on the load capacity of the towing vehicle
Technical information
System basic 1.1
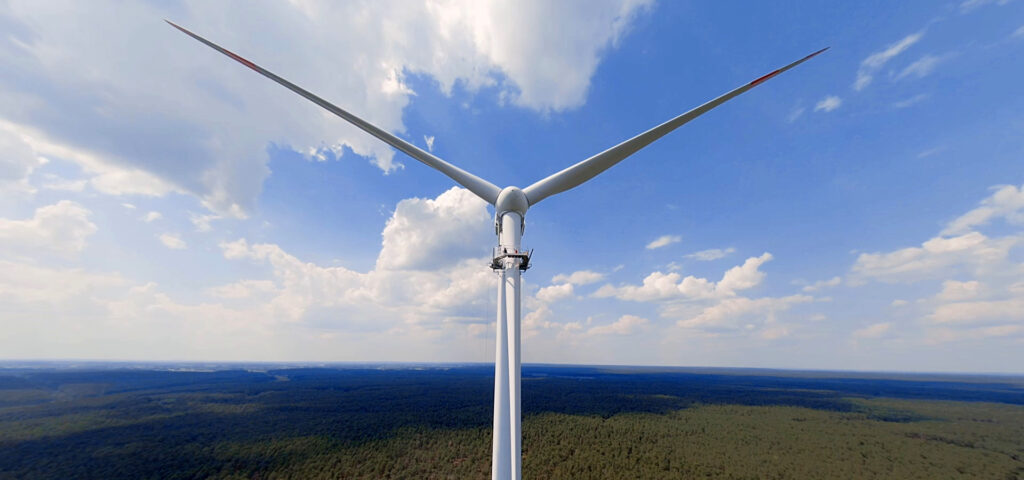
Dependable. No job too big.
Blade accessibility
Maintenance platform can be swivelled and moved sideways (± 500 mm)
Winching speed
8 m/min
Winches/emergency arresting devices
Tirak / Blocstops
Max. rotor blade dimensions
4.90 m x 3.20 m
Max. distance between tower and blade tip
15 m
Max. wind turbine height
180 m (contact us to discuss taller turbines)
Max. wind speed
14 m/s
Self-adjusting suspension structure
Adjusts to distances between attachment points ranging from 1,7 m to 4,0 m
Inclination adjustment
Simple inclination adjustment by the user
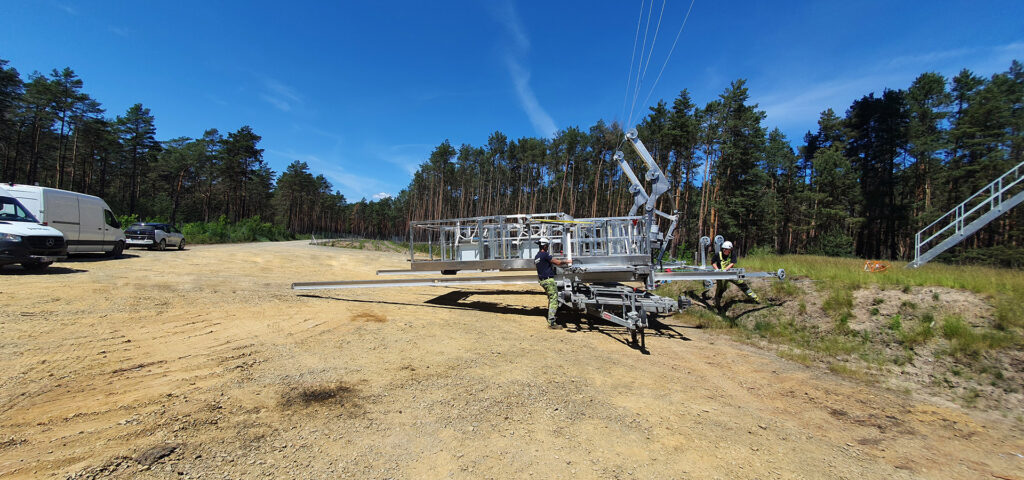
Dependable. No job too big.
Dimensions in transport mode
9,00 m x 2,55 m x 3,90 m
Tare weight
1800 kg
Loading capacity
400 kg (max. 3 people)
Transport
Specially built tandem trailer